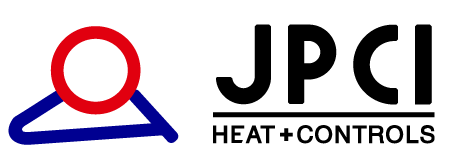
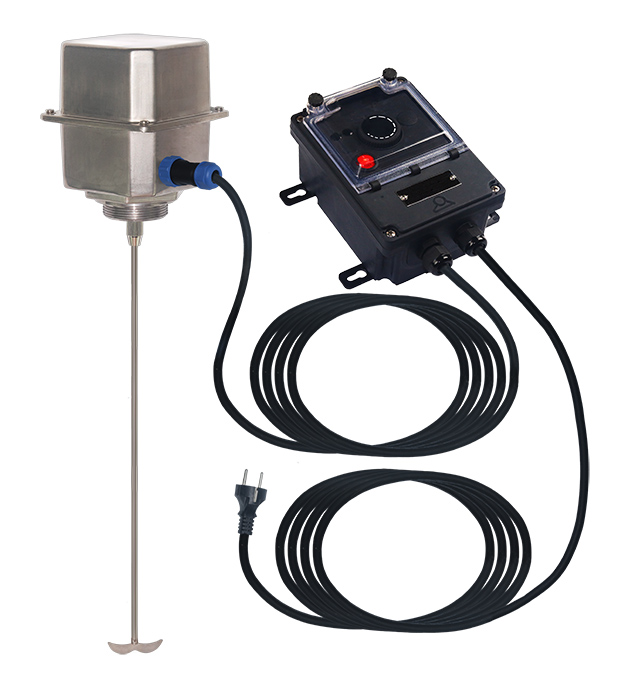
- Air and Fluid heating solutions
- Industry
- Agriculture and Farming
- Petrochemistry
Main Features
Reheating by jacket heaters of barrels and bulk container type IBC is often slowed by the duration of temperature homogenization, when low-viscosity or low thermal conductivity fluids are used. Deviations of more than 20°C are very often found during heating between the different areas of these containers. The use of a stirrer makes it possible to shorten the reheating time by increasing the speed of the heat transfer at the walls and by equalizing the temperature. This stirrer is screwed onto the 2" threaded filling port of the 30-gallon (100-liter) and 55-gallon (220-liter) metal drums. In the case of bulk containers (IBC), whose filling orifice comprises a plastic cap of variable size according to the manufacturers (100 to 150mm), it is necessary to make a hole of 60mm in this cap and to tighten the stirrer in this hole by a locknut.
Adjustment of its rotation speed is achieved by a low voltage DC supply. This power supply is located in a remote box, connected by a 3m cable equipped with a quick connector.
The rotation speed must be adapted to the viscosity of the fluid. We recommend using this stirrer only when the temperature of the heated fluid is 10 to 20°C below the chosen reheating temperature. The stirrer should not be run in frozen or too viscous products as this will trip the fusible overcurrent protection system.
Stirrers come in two versions: with and without built-in temperature sensor. The temperature sensor allows to check the temperature at the center of the heated product.
The shaft of the stirrer can be disassembled for replacement or to be shortened.